Plastic dryers are the most effective and economical models for drying plastic raw materials. They can dry raw materials that are damp due to packaging, shipping, or recycling. The hopper is made of stainless steel and has the functions of "hot air blowing down" and "cyclone exhaust" and double-layer insulation barrels, which is especially suitable for drying engineering plastic materials with a dehumidifier.
Plastic dryer Dryer characteristics1. Adopt P.I.D temperature control system, precise temperature control;2. The unique down-blowing air pipe design can evenly distribute the hot air, keep the plastic dry, stabilize the temperature, and improve the drying efficiency; 3. Stainless steel double-layer insulation barrel and attached window; 4. Widely GHD-40U and above models are equipped with openable door; 5. Thermal overload protection device, safe and reliable; 6. Novel appearance and bright appearance;
Plastic dryer working principleThe air blown by the drying fan becomes high-temperature dry air after drying and electric heating. Through the unique lower blowing tube design, the hot air is evenly dispersed in the thermal insulation barrel to dry the raw materials; optional hot air recovery device, the blown wind is filtered and then dried The wind blows out, forming a closed loop.
Plastic dryer What models
Stand-alone(Plastic dryer) |
2 machine 1 body dryer |
3 machine 1 body dryer |
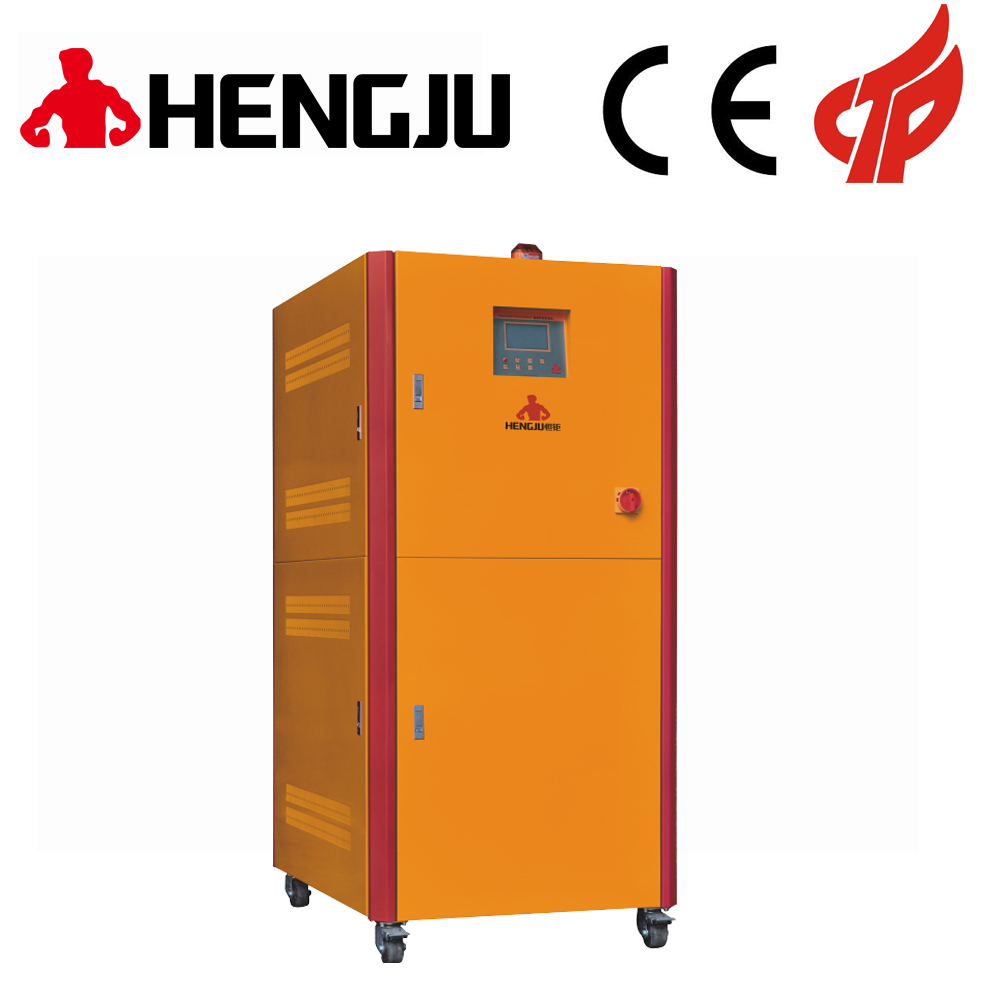 |
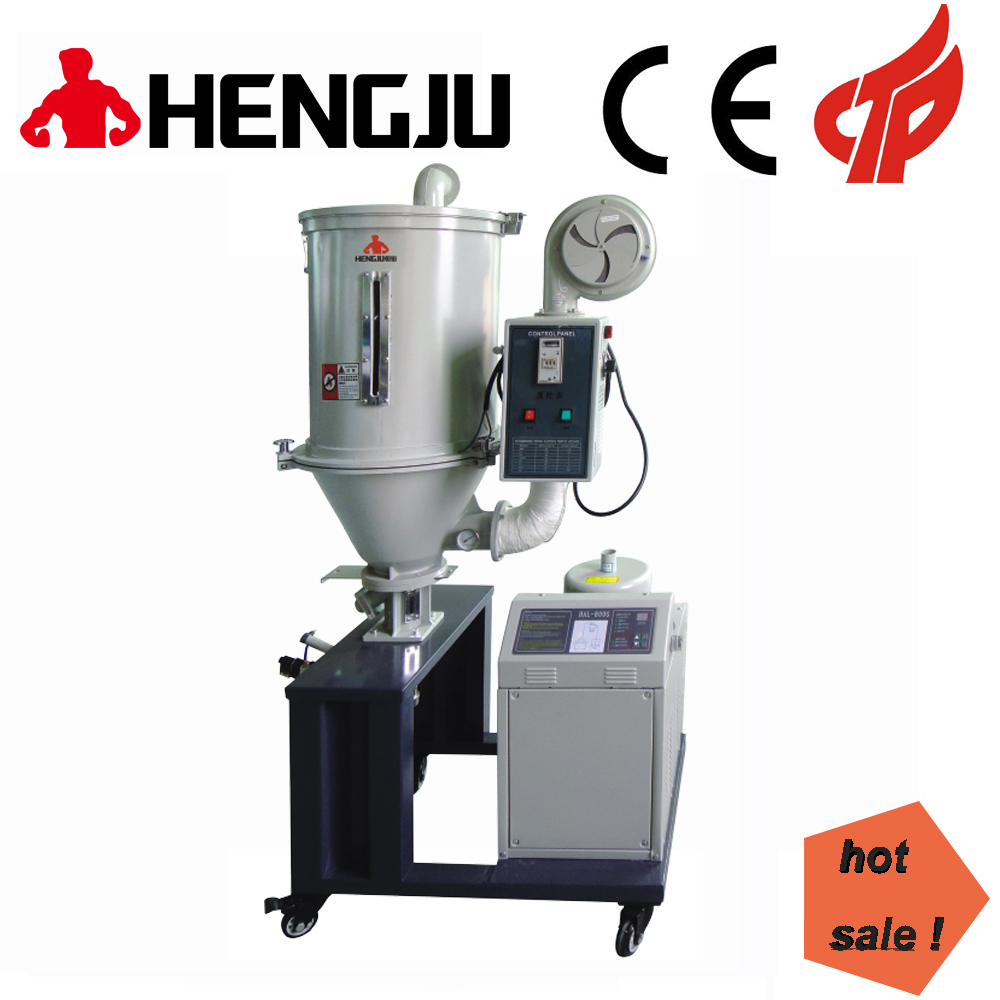 |
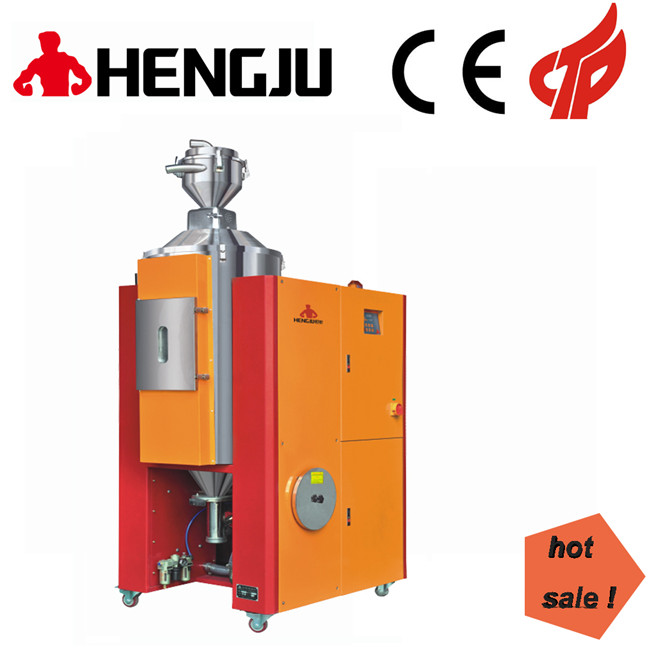 |
1 Plastic dryer-Dehumidifying Dryers
Dehumidifying Dryers are designed to eliminate moisture in the plastic material before processing. Air is forced through a desiccant bed to make it extremely dry. This air is then heated to a specified temperature and fed into a Drying Hopper containing the material to be dried. This hot dry air draws the moisture out of the material; the saturated air is then fed out of the Drying Hopper and back through the desiccant bed again to remove the moisture before the cycle begins again. This desiccant has a limited ability to hold moisture before it needs to be regenerated (dried out). Typically, plastics processors use regenerative or twin tower dryers and in this case, when the desiccant bed has reached its moisture retaining capacity the airflow is automatically switched to the second desiccant bed to allow the drying process to continue. At the same time, the first desiccant bed is regenerated by heating to remove moisture, allowed to cool and it is then ready to absorb moisture again.
2 Plastic dryer-Rotary Wheel Dryers
Rotary Wheel Dryers have been designed to address energy and other revenue draining issues presented by other types of drying. Rotor Dryers have a constant dew point whereas in twin desiccant dryers the dew point starts very low but increases as the desiccant bed saturates. When the airflow is switched to the second desiccant bed the dew point starts low again. Dew point control is a design feature of Rotor Dryers which allows the user to select a dew point suitable for the material to be processed and maintain this. This is a particularly beneficial feature as it virtually eliminates over drying. Some models of Rotor Dryers can save up to 40% in energy consumption when compared with the most efficient twin desiccant dryers, due to a lower regeneration temperature. This figure depends on the manufacturer of the dryer and can be less when only a 3-stage circuit technology is part of the design. 4 stage technology is available. Rotor Dryers utilise a rotating wheel which continuously puts dry desiccant into service due to its ability to regenerate moisture saturated desiccant in the same rotational cycle. Whereas the desiccant bed used in traditional Dehumidifying Dryers comprises desiccant beads and clay binder which degrades, Rotary Wheel Dryers employ in the region of 3 times the amount of pure desiccant. Desiccant beds on twin tower Dehumidifying Dryers regenerate at 320c, however in the Rotor Dryer it is an energy saving 140c. They do not use chilled water and they do not require compressed air. Central Drying System
3 Plastic dryer-Low Pressure Dryers or Vacuum Dryers
Low Pressure Dryers or Vacuum Dryers accelerate the plastic material drying process by using a vacuum to lower the boiling point of water from 100 °C to 56 °C. The moisture is rapidly extracted from the heated material. Leaving it in a condition to be moulded or extruded. Typically, these Low Pressure Dryers will dry materials in one-sixth of the time required by a desiccant dryer and the use of vacuum provides many process and revenue benefits when compared with conventional drying methods. This method of drying does not use desiccant at all and as such not only saves the expense but also saves the time required to maintain and replace desiccant. The low drying times offered by these machines reduces the risk of material degradation from exposing material to prolonged elevated drying times. LPDs - Cleanroom Application
4 Plastic dryer-Compressed Air Dryers
Compressed Air Dryers, compact and light in weight these Dryers are designed to fit to the throat of the processing machine, although a free standing frame can be employed. Generally a method of drying employed for smaller throughput machines, the Compressed Air Dryer is similarly equipped with twin desiccant beds as the Dehumidifying Dryer. The main difference between the two is that air flow is generated by compressed air instead of electrically driven mechanical blowers.
5 Plastic dryer-Hot Air Dryers
Hot Air Dryers are designed to remove surface moisture from no-hygroscopic material and to pre-heat material prior to processing. This pre heating is particularly useful in circumstances where material has been stored outside in the cold and is brought into more warm and humid conditions for processing. They usually comprise a well insulated hopper with an attached blower and heater. Hot air is blown through the material granules and the wet air is dispelled into the atmosphere.
Plastic dryer-Applied material parametersIt is suitable for the drying and cooling of powdery and granular materials in chemical, pharmaceutical, food, food, dehydrated vegetables, minerals and other industries. Before using the equipment, you need to check the plastic dryer before starting it. This is also a daily necessary preparation. First check whether there is any looseness in the connection between the bearing and the sealing part of each equipment, the lubricating oil status of each mechanical component, and whether the water, wind, and slurry pipe valve ports are in the desired orientation.
Plastic material |
Dryer |
Density(kg/dm3) |
Drying time(h) |
Drying temperature(℃) |
Atmospheric flow(m3/kg) |
Moulding moisture content(%) |
Initial moisture contnt(%) |
ABS料 |
√ |
0.55 |
2-3 |
85 |
2 |
<0.020 |
< 0.2 |
CAB 料 |
√ |
0.60 |
2-3 |
70 |
2 |
<0.020 |
< 0.6 |
EVA(2)料 |
√ |
0.60 |
2-3 |
90-105 |
1.8 |
- |
- |
EVOH料 |
√ |
0.60 |
2-3 |
90-105 |
2 |
- |
- |
LM(4)料 |
√ |
0.50 |
3 |
600 |
2 |
<0.080 |
<0.2 |
LCP料 |
√ |
0.80 |
3-4 |
150 |
2.2 |
< 0.01 |
<0.05 |
PA11料 |
√ |
0.60 |
3-5 |
70-80 |
2 |
- |
0.6-1.2* |
PA6.46.6料 |
√ |
0.60 |
4-6 |
70-80 |
2 |
0.15-0.02* |
0.6-1.2* |
PAI料 |
√ |
0.85 |
6-8 |
180 |
2 |
<0.02 |
- |
PAR料 |
√ |
0.70 |
5-6 |
120 |
2 |
<0.02 |
- |
PBT料 |
√ |
0.80 |
3-4 |
130-140 |
2.2 |
<0.02 |
< 0.15 |
PC料 |
√ |
0.65 |
2-3 |
120 |
2 |
< 0.02 |
< 0.3 |
PC/ABS料 |
√ |
0.65 |
42798 |
100 |
2 |
< 0.020 |
<0.1 |
PC/PBT料 |
√ |
0.75 |
3-4 |
110 |
2.2 |
- |
- |
PE.HDEPE.LDPE black3%料 |
√ |
0.50 |
1 |
85 |
1.6 |
<0.01 |
<0.02 |
PE.HDEPE.LDPE black40% 料 |
√ |
0.70 |
2-3 |
80-90 |
2 |
<0.02 |
<0.2 |
PEEK料 |
√ |
0.80 |
3-4 |
150-160 |
2.2 |
<0.05 |
<00.1 |
PE(1)(3)料 |
√ |
0.75 |
4-5 |
140-160 |
2.5 |
<0.01 |
<0.2 |
PEN(1)(3)料 |
√ |
0.86 |
5-6 |
150-170 |
3 |
<0.005 |
- |
PES料 |
√ |
0.80 |
3-4 |
150-180 |
2 |
<0.05 |
0.35 |
PET料 |
√ |
0.84 |
5-6 |
160-180 |
3 |
<0.003 |
< 0.2 |
PETG料 |
√ |
0.74 |
4-5 |
65 |
3.5 |
<0.01 |
<0.1 |
PI料 |
√ |
0.70 |
2-3 |
120 |
2.2 |
<0.02 |
- |
PMMA-料 |
√ |
0.65 |
3-4 |
80 |
3 |
< 0.02 |
<0.3 |
POM料 |
√ |
0.85 |
2-3 |
90-100 |
2 |
- |
<0.15 |
PP料 |
√ |
0.50 |
1 |
80-90 |
2 |
- |
- |
PPO料 |
√ |
0.55 |
2 |
100-110 |
2 |
<0.01 |
- |
PPS料 |
√ |
0.80 |
2-3 |
130-140 |
2 |
<0.01 |
<0.03 |
PS[GPPS.EPS.HIPS]料 |
√ |
0.55 |
1 |
80 |
1.7 |
<0.02 |
<0.05 |
PSU料 |
√ |
0.80 |
3-4 |
120-130 |
2 |
<0.05 |
<0.1 |
PIT料 |
√ |
0.80 |
5-6 |
130-150 |
3 |
<0.05 |
<0.2 |
PUR料 |
√ |
0.75 |
2-3 |
70-90 |
2 |
<0.02 |
- |
PVC料 |
√ |
0.85 |
1 |
70-80 |
1.4 |
<0.02 |
- |
SAN料 |
√ |
0.55 |
2-3 |
80 |
2 |
<0.02 |
<0.1 |
SB料 |
√ |
0.60 |
1-2 |
80 |
2 |
<0.02 |
- |
TPE料 |
√ |
0.65 |
2-3 |
110 |
2.2 |
<0.05 |
<0.3 |
TPE料 |
√ |
0.65 |
2-3 |
80 |
2.2 |
< 0.1 |
- |
TPO料 |
√ |
0.55 |
3 |
70-90 |
2 |
- |
- |
TPU料 |
√ |
0.75 |
2-3 |
70-100 |
2 |
< 0.02 |
- |
Plastic dryer The factors that affect the drying effect are:Drying temperature: Heat is the key to opening the joint force between water molecules and hygroscopic polymers. When it is higher than a certain temperature, the attraction between the water molecules and the polymer chain will be greatly reduced, and the water vapor will be taken away by the dry air. Dew point: In the dryer, first remove the humid air to make it contain very low residual moisture (dew point). Then, by heating the air to reduce its relative humidity. At this time, the vapor pressure of dry air is low. By heating, the water molecules inside the particles get rid of the binding force and diffuse to the air around the particles. Time: In the air around the particles, it takes a certain time for the absorption of heat and the diffusion of water molecules to the surface of the particles. Therefore, resin suppliers should specify the time it takes for a material to effectively dry at the proper temperature and dew point. Airflow: Dry hot air transfers heat to the particles in the drying silo, removes the moisture on the surface of the particles, and then sends the moisture back to the dryer. Therefore, there must be sufficient airflow to heat the resin to the drying temperature and maintain this temperature for a certain period of time.
Plastic dryer maintainTurn on the power and check whether the voltage and surface of the high-efficiency plastic dryer are normal. After all, check the amount and concentration of the slurry in the slurry mixing barrel. If there is a problem, it should be cleaned in time. 1. Before each operation, the operator should check whether the steam valve, compressed air and each range meter are normal. 2. Check whether the air pressure of the upper and lower airbag seals is below 0.1 ~ 0.15mpa. If the air pressure is too high, the seal will burst, and if it is too low, the powder will not leak from the seal, which will affect the output power and dry quality. 3. Check whether the upper and lower airbag seals have protrusions and the flat head screws are loose to prevent the material truck from crashing when it is pushed in. 4. Check whether the blade of the hopper is too tight. The blade is too tight and the resistance of the material constitutes the addition of the transmission load of the mixing motor, causing the transmission bump to break or the motor to burn.
Efficiency and service life of the equipment are inseparable from daily maintenance and use, and the staff must not be underestimated. When the problem of poor drying occurs, the problem should be found from the following three aspects:
1. Plastic dryer Condition of the dryerWhen inspecting the dryer, pay special attention to the air filter and hose. A clogged filter or flattened hose will reduce the air flow, thus affecting the operation of the dryer; A damaged filter will contaminate the desiccant, inhibiting its ability to absorb moisture; a broken hose may introduce moist ambient air into the drying airflow, causing the desiccant to absorb moisture prematurely and high dew point; poorly insulated hoses and drying The silo also affects the drying temperature.
2.Plastic dryer Dry air pathIn the drying air circuit, the drying temperature should be detected at the inlet of the silo to compensate for the heat loss of the dryer in the hose. The air temperature at the inlet of the silo is low, which may be due to improper adjustment of the controller and lack of insulation layer, or the heater element, heater current contactor, thermocouple or controller have failed. In addition, it is also important to monitor the drying temperature throughout the drying process and observe the temperature fluctuations during desiccant replacement. If the material is not properly dried after coming out of the dryer, you should check whether the drying bin has enough space to provide sufficient and effective drying time. The effective drying time refers to the time when the particles are actually exposed to the appropriate drying temperature and dew point. If the residence time of the granules in the silo is insufficient, proper drying cannot be achieved. Therefore, attention should be paid to the size and shape of the granular material or crushed material, which will affect the bulk density and residence time of the dried material. A twisted hose or a clogged filter can restrict airflow and affect the performance of the dryer. Therefore, if the dryer does not find such problems, it is impossible to judge whether the airflow is sufficient. Here, there is a quick, simple and accurate method to detect whether the airflow of the dryer is sufficient, that is, to measure the vertical temperature curve of the material in the drying bin. It is assumed that the drying time recommended by the material supplier is 4h, and the processing capacity is 100lb / h (1lb = 0.4536Kg). To determine whether the airflow of the dryer is sufficient, you can measure the temperature curve in the drying bin. Here, pay special attention to the temperature at 4h (400lb). If the temperature at the 400 lb level in the drying bin reaches the set value, then the air flow can be considered sufficient. If only the materials at 1h, 2h or 3h in the drying silo are fully heated, it means that the gas flow cannot complete the heating and drying of the materials at the predetermined yield. Insufficient heating may indicate that for this productivity, the drying silo is too small, or the air flow is restricted due to clogged filters or damaged hoses. If the air volume is too large, there will be problems, which not only waste energy, but also cause the temperature of the return air to be high and destroy the performance of the desiccant. The return air filter can prevent the filamentous material from contaminating the desiccant and affecting its hygroscopic performance. These filters must be kept clean to ensure adequate airflow. When the drying air comes out of the top of the dryer, most of the heat has been released. When the desiccant temperature is in the range of 120oF ~ 150oF, most dryers can work efficiently. If the return air overheats the desiccant, it will reduce its ability to adsorb moisture in the dry air. Always check the return air temperature of the dryer. When the temperature of the return air is high, it may indicate that for this productivity, the size of the dryer is too large, or the temperature when the material enters the drying bin is high, for example, PET has crystallized before drying, or only certain materials (such as PET ) The drying temperature is higher than the normal temperature range. In order to prevent the return air temperature from becoming high, as long as a heat exchanger is installed on the return air path, it can ensure that the desiccant can effectively remove the moisture in the dry air.
3.Plastic dryer Regeneration and cooling of desiccantThe moisture absorption capacity of the desiccant is limited, so the moisture it absorbs must be removed by regeneration. The process is: when the ambient air is sucked in, it enters the blower through a filter and is then sent to a group of heaters. The heated air passes through the desiccant bed. When the temperature of the desiccant rises, the adsorbed moisture is released. When the hot air is saturated with water vapor, it is discharged into the atmosphere. The high-temperature regenerated desiccant must be cooled before returning to the drying loop to restore the desiccant's moisture absorption function. The dew point reading can help find some problems, so the dry air dew point value should be monitored throughout the drying process. The dew point reading of the dryer during normal operation should be a straight line in the range of 20oF ~ 50oF. Of course, the small fluctuations caused by the replacement of the desiccant are normal. If the dryer is operating normally, the dew point at the dry air inlet should be at least 30oF lower than the dew point at the return air outlet. On the other hand, after the desiccant was replaced, the dew point peaked immediately, indicating that the desiccant was not sufficiently cooled before being placed, making it unable to absorb moisture well. After cooling, the dew point of the desiccant will drop to the normal standard. If the desiccant is not properly cooled, the temperature will peak, and the sudden temperature change will reduce the drying ability of the desiccant on heat-sensitive materials such as ionomers, amorphous polyester and certain nylon brands. If the dew point reading is normal after the desiccant bed is replaced, but the dew point rises quickly before the desiccant drying cycle ends, it means that ambient air may have entered the closed air path, causing the desiccant to absorb moisture prematurely. Another possibility is that the desiccant regeneration is incomplete or contaminated. If the dew point reading and the return air dew point reading are close, it indicates that the regeneration air circuit is completely invalid or the desiccant is seriously polluted.
|